Wie können reale Maschinen- und Prozessdaten die Produktion effizienter und innovativer machen? Von präzisen Verschleißprognosen für Fräswerkzeuge bis hin zur Nutzung flexibler Datenräume zeigt Fed-X-Pro, wie datengetriebene Anwendungen die Fertigung der Zukunft gestaltet. Erfahren Sie, wie Technologien wie GAIA-X, digitaler Zwilling und Low-Code-Plattformen neue Standards setzen – und wie aus Theorie praxisnahe Lösungen werden.
Lesen Sie weiter und entdecken Sie, wie Fed-X-Pro die Produktion neu denkt.
Was ist im Projekt geschehen?
Datenaufnahme & Versuche
Ziel des Projektes Fed-X-Pro war es, am Beispiel neuartiger datengetriebener Produkt-Service-Anwendungen für hochwertige Zerspanwerkzeuge den Mehrwert vernetzter, unternehmensübergreifender Datenräume unter Beachtung des Datenschutzes und der Datensouveränität für die industrielle Fertigung zu demonstrieren (lesen Sie auch hier). Eine Anwendung war dabei, bezogen auf Fräswerkzeuge, Prognosen über die Standzeiten, d. h. der Lebensdauer der beim Zerspanen eingesetzten Werkzeuge unter ihren ganz individuellen Bedingungen vorausschauend tätigen zu können.
Datenlieferanten lieferten dabei unterschiedlichste Maschinen- und Werkzeugdaten aus der Fertigung, die steuerungsseitig mittels OPC UA bereitgestellt wurden. Für die Erfassung der Datenpunkte aus dem Fertigungsprozess wurde die von Fraunhofer entwickelte LinkedFactory verwendet. Diese ermöglicht es, Prozessdaten aus verschiedenen Datenquellen (wie SAP, SQL, OPC UA) zu erheben und mit zusätzlichen Informationen (wie z. B. Herkunftsinformationen oder Maßeinheiten) zu verknüpfen und in einer Zeitreihendatenbank persistent abzulegen.
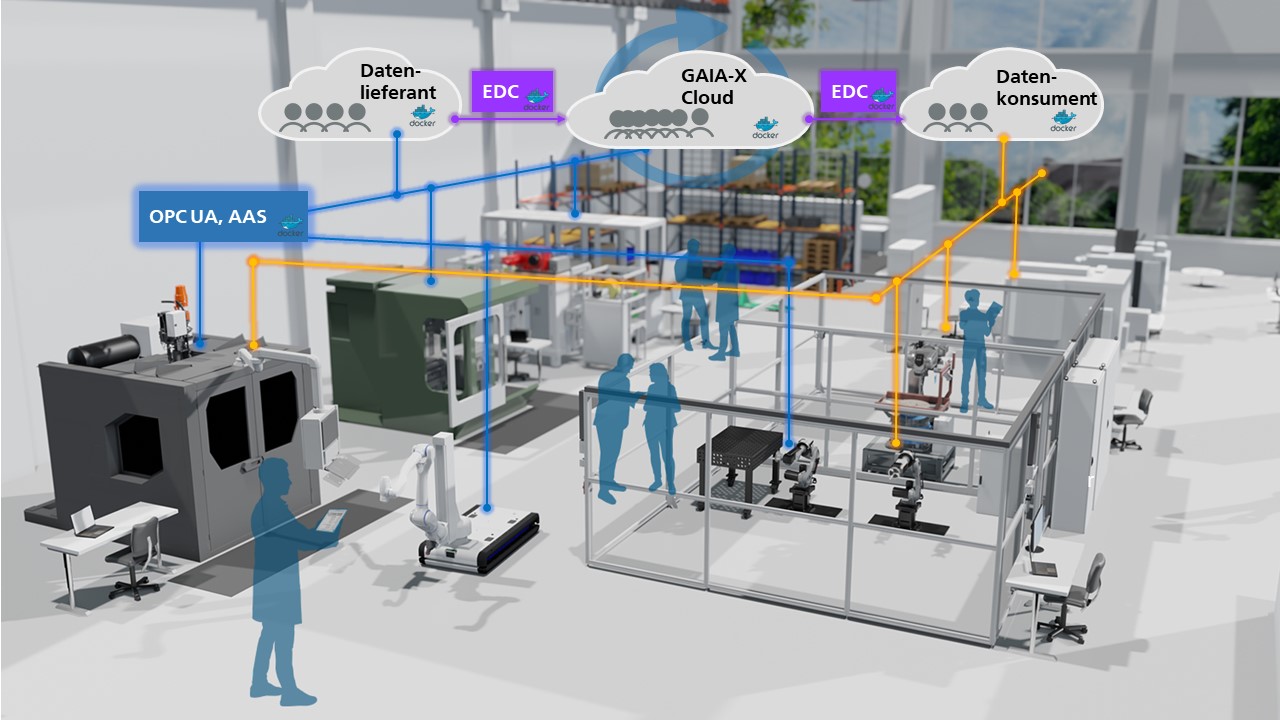
Überführung der Theorie in die Praxis
Auf der Versuchsfeldmaschine MAHO in unserem Versuchsfeld auf der Pforzheimer Straße wurden mithilfe der oben genannten Datenpipeline Messdaten aufgenommen. Hierbei bestand die Aufgabe, den Verschleiß vom Bohrer über den Spindelstrom sichtbar zu machen. Insgesamt 800 Bohrlöcher wurden in eine hochlegierte Stahlplatte gebohrt. Die Bohrer und die entsprechenden Parameter hat dabei der Werkzeughersteller Gühring KG bereitgestellt. Der Verschleiß am Werkzeug wurde aller 25 Bohrungen unter dem Mikroskop dokumentiert und entsprechend vermessen. In der folgenden Abbildung ist mittig die Versuchsmaschine MAHO dargestellt. Oben links sind Spindelstrom, -geschwindigkeit und die Achspositionen im Messverlauf von 25 Bohrlöchern zu sehen. Rechts daneben ist die vollständig gebohrte Stahlplatte zum Versuchsende dargestellt. Die beiden Abbildungen der Bohrspitze (unten) zeigen die Werkzeugverschleiß nach den Testbohrungen.
Dieser Versuch wurde bei den Partnern UKM technologies GmbH und Gühring KG auf anderen Fräsmaschinen wiederholt. Dadurch konnte ein vielfältiger Datensatz gewonnen werden, auf dessen Basis ein KI-Modell (Katulu GmbH) zur Vorhersage der Werkzeuglebensdauer trainiert werden konnte.
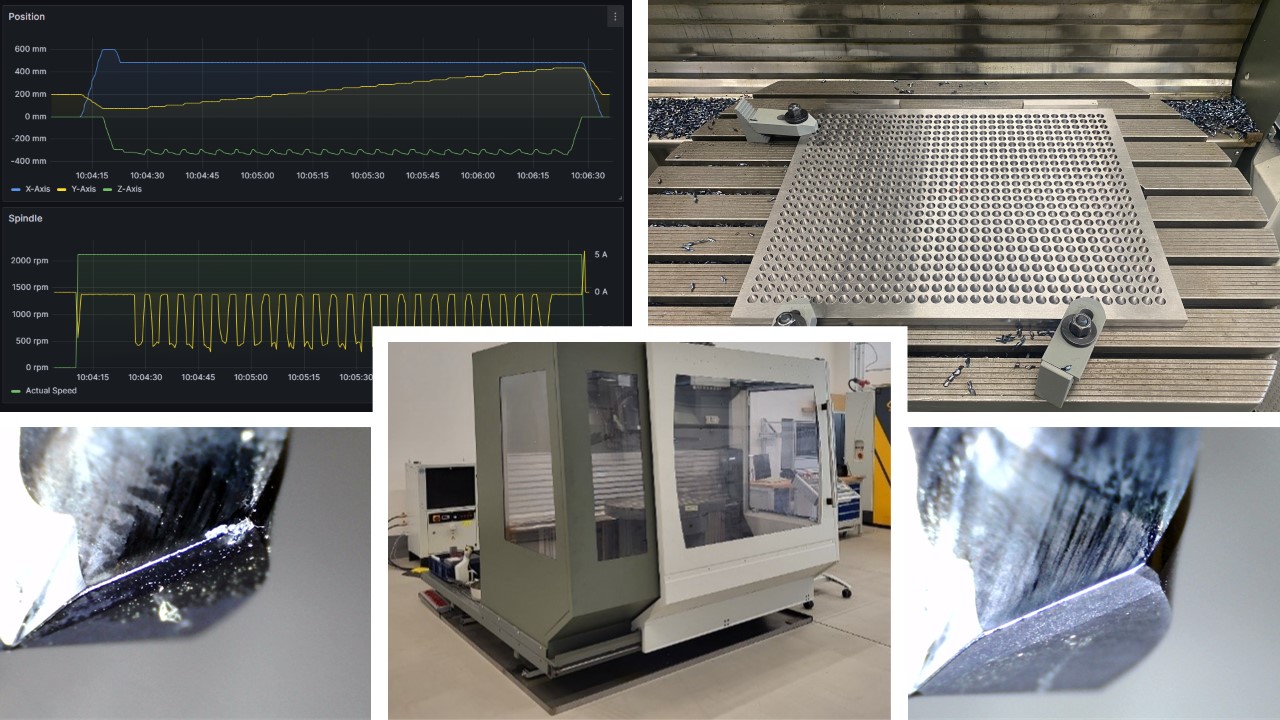
Datenweiterleitung & -nutzung
Die AAS, oder Verwaltungsschale, ist ein digitaler Zwilling, der alle wichtigen Informationen und Daten einer Maschine oder eines Produkts in der Industrie enthält und zugänglich macht. Im Projekt wurden die Struktur der Fräsmaschine als Informationsmodell als auch die für die Datenerfassung relevanten OPC UA-Zugriffspunkte dargestellt und gespeichert.
Im Kern der entwickelten Datenverarbeitungspipeline stand der Eclipse Dataspace Components Connector (EDC Connector), der als Verbindungsstück und Vermittler für den Zugang zum Datenraum verantwortlich ist. Dieser ermöglicht eine GAIA-X konforme, d. h. vertrauenswürdige und souveräne Dateninfrastruktur. Innerhalb des Unternehmens werden Maschinendaten mithilfe der Verwaltungsschale (AAS) an den EDC angebunden.
Zum Verteilen und Bereitstellen der einzelnen Softwarekomponenten wurde Docker verwendet: eine Plattform, die es ermöglicht, Anwendungen in sogenannten Containern zu verpacken. Docker bietet den Vorteil, dass Anwendungen in Containern überall konsistent laufen, was die Portabilität und Effizienz verbessert, da Container leichtgewichtig sind und weniger Ressourcen als virtuelle Maschinen benötigen. Dies ermöglicht eine Installation aller Komponenten mit nur einem Befehl und erleichtert so auch deren Verwaltung.
Datenkonsumenten wie Dienstleister können mit ihren Konnektoren auf den gemeinsamen Datenraum zugreifen, um Anwendungen zu entwickeln. Solche Dienstleister können beispielsweise KI-Dienste, wie der im Projekt genutzte Federated Learning Ansatz der Katulu GmbH oder Low-Code Ansätze, wie die Plattform der Simplifier AG sein. Der Datenanbieter behält dabei, unabhängig vom Anwendungsfall, die Kontrolle über seine Daten und kann die Expertise der Dienstleister zur Wertschöpfungssteigerung der eigenen Produktion nutzen.
Haben wir Ihr Interesse geweckt? Wenn Sie mehr über Datenräume, die Erfassung von Maschinendaten oder die Vernetzung verschiedener Datenquellen erfahren möchten, stehen wir Ihnen jederzeit gerne zur Verfügung. Kontaktieren Sie uns und lassen Sie uns gemeinsam Ihre Datenwelt vernetzen und optimieren!
👉 Jetzt mehr erfahren und Kontakt aufnehmen!