Neuartiger Digitaler Zwilling bildet die Belastung der Strukturkomponenten von Pressen ab
In der Produktionstechnik existieren viele Definitionen für einen Digitalen Zwilling. Besonders häufig wird die Abbildung kinematischer und geometrischer Eigenschaften von Maschinen und Anlagen in ihrer Wechselwirkung als Digitaler Zwilling beschrieben und für Inbetriebnahmen oder Variantenstudien genutzt. Dass dies noch lange nicht die letzte Ausbaustufe der Informationsdichte innerhalb dieses virtuellen Maschinenabbildes ist, zeigen die Forschenden am Fraunhofer IWU.
Im Bereich Umformmaschinenentwicklung konnte ein Digitaler Zwilling entwickelt werden, der neben den geometrischen Eigenschaften auch die elasto-mechanischen Reaktionseigenschaften von Strukturkomponenten repräsentiert. Dieser spezielle Digitale Zwilling von Pressen ist somit in der Lage, bspw. die Gestellbelastung während des Betriebes der Presse zu beschreiben und verfügbar zu machen. Dies gilt neben quasistatischen Belastungen (vor allem Großpressen werden prozessseitig häufig langsam belastet) auch für dynamische Belastungen, welche bei Schnellläuferpressen oder bei dynamischen Umformoperationen wie dem Schneiden auftreten.
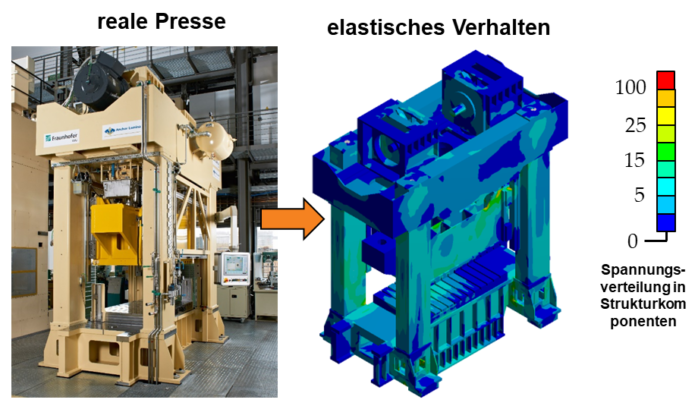
Virtuelle Sensoren als Enabler für Inline-Fähigkeit
Echtzeitfähigkeit ist ein wesentliches Kriterium bei der Realisierung von Überwachungssystemen zur Schadensvermeidung. Vielschichtige Auswerteroutinen sind dafür oftmals hinderlich, sobald diese On-Prem ausgeführt werden sollen. Daher ist eine komplexe Beschreibungsform des Digitalen Zwillings für derartige Systeme nicht prädestiniert. Diese Komplexität kann durch die Nutzung virtueller Sensoren aufgelöst werden. Dabei wird eine Kombination aus an der Maschine verbauten Sensoren und einzelnen, weniger komplexen, Auswertealgorithmen genutzt. So werden insbesondere kritische Bereiche von Strukturkomponenten an Pressen überwacht. Dies geschieht dann ohne an diesen Stellen reale Sensoren verbauen zu müssen. Die On-Prem umzusetzenden Berechnungsaufgaben beschränken sich dann auf wenige Gleichungen, mit denen die virtuellen Sensoren gebildet werden. Für eine Kalibrierung dieser virtuellen Sensoren wird der Digitale Zwilling der Maschine genutzt. Somit ist ein besonders effizientes Vorgehen zur Integration möglich, ohne umfangreiche Messungen an der Presse durchzuführen.
Nachrüstung kognitiver Fähigkeiten
Das beschriebene Konzept ermöglicht eine schnelle Nachrüstung dieser virtuellen Sensoren. Somit kann mit überschaubarem Aufwand eine Umformmaschine mit kognitiven Fähigkeiten ausgerüstet werden. Die Überwachung der Beanspruchung der Strukturkomponenten kann dann genutzt werden, um kontinuierlich zu bewerten, ob die Presse im aktuellen Produktionsschritt kritisch oder unkritisch belastet wird. Somit können auch derart komplexe Maschinen künftig wissensbasiert sicher bis an ihre tatsächliche Leistungsfähigkeit betrieben werden, ohne einen Schaden zu fürchten.
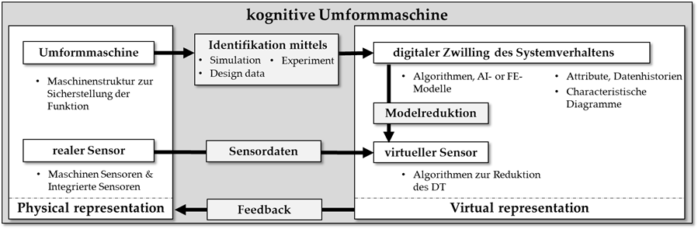
Smart Maintenance Community
Dieser Beitrag stellt eine Möglichkeit der präventiven Instandhaltung vor. Weitere Ansätze und Lösungen mit ähnlichen Zielstellungen werden in der Smart Maintenance Community umgesetzt. Die wichtigsten Eckdaten dieses Zusammenschlusses von derzeit 12 Fraunhofer-Instituten und eine Vorstellung der verschiedenen Level von Instandhaltungsstrategien lesen Sie in unserem Auftaktbeitrag zum Thema der Smart Maintenance Community hier. Die Beiträge zu weiteren Projekten im Kontext der Smart Maintenance Community sind hier zu finden.
Vom Labor in die Praxis
Die beschriebene Lösung konnte am Fraunhofer IWU erfolgreich getestet werden und wird aktuell an mehreren Pressen in Produktionsumgebungen integriert. Dabei werden neben den beschriebenen Möglichkeiten auch Quereffekte für eine Nutzung zur Prozessüberwachung analysiert.
Für Rückfragen und Anmerkungen steht Ihnen Herr Robin Kurth als Gruppenleiter “Umformmaschinen” gerne via LinkedIn oder unter folgender Mailadresse zur Verfügung: robin.kurth@iwu.fraunhofer.de.
Headerbild: © Fraunhofer IWU