Auslastungsoptimierung ist eine Anforderung der Produktion
Neben klassischen Bewertungsfaktoren wie Produktivität und Effizienz spielen die Faktoren Flexibilität und Reaktionsvermögen eine immer bedeutsamere Rolle. Weite Bereiche der Produktion sind derzeit von hochspezialisierten Systemen und starren Abläufen geprägt. Dieser Aspekt steht den Forderungen nach Anpassungsfähigkeit und Individualisierung entgegen.
Um diesen Herausforderungen zu begegnen und dabei neue Wege für die Produktion der Zukunft aufzuzeigen, arbeiten Institute der Fraunhofer-Verbünde “Produktion“, “Light & Surfaces” und “IuK” im Leitprojekt »SWAP« zusammen. Dabei werden vier industrierelevante Use-Cases aus den Bereichen Fertigung, Montage, Logistik und Qualitätssicherung betrachtet. Ziel ist die Untersuchung und Entwicklung heterogener, auslastungsoptimierter Roboterteams und Produktionsarchitekturen.
Use Case Großbauteilfertigung
Das Fraunhofer IWU befasst sich im Use-Case »Großbauteilfertigung« mit der Entkopplung von Werkstückgröße und notwendigem Arbeitsraum. Ziel ist hierbei die Reduktion des Bedarfs an kostenintensiven, hochspezialisierten und unflexiblen Großwerkzeugmaschinen. Erreicht wird dies durch eine Aufteilung des Großbauteils in kleinere Einzelsegmente, die aufgrund ihres geringeren Bauraumbedarfs auf konventionellen Werkzeugmaschinen und Robotern gefertigt werden können. Die Aufteilung des Großbauteils wird – im Sinne des übergeordneten Projektziels Auslastungsoptimierung – unter Verwendung verschiedener Optimierungsalgorithmen bedarfsgerecht vorgenommen. Unter dem Stichwort bedarfsgerecht wird in diesem Kontext die Ermittlung und Verteilung einer Kombination von Einzelsegmenten verstanden, welche optimal auf die Eigenschaften und Fähigkeiten – bspw. Bauraum oder Achskonfiguration – der verfügbaren Feldkomponenten zugeschnitten ist. Gleichzeitig sollen die notwendigen Randbedingungen hinsichtlich Qualität, Festigkeit, Fertig- und Montierbarkeit eingehalten werden. Die ursprüngliche Zielgeometrie des Großbauteils wird anschließend durch robotergeführtes oberflächennahes Fügen der Einzelsegmente und eine globale Finishbearbeitung durchgeführt. Dafür wird eine an das Bauteil gekoppelte mobile Maschinen genutzt.
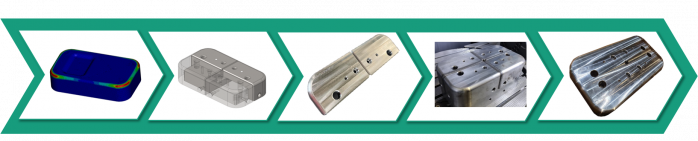
Entwicklung erster Proof of Concept
Derzeit wird ein erster Proof of Concept der dargelegten fertigungstechnischen Prozesskette entwickelt. Als Demonstrationsobjekt dient dabei der Stempel eines einfachen Umformwerkzeugs. Dieser untersucht stellvertretend die Anwendbarkeit im Bereich hochbelasteter Großbauteile – bspw. im Karosseriebau. Dieser Werkzeugstempel wurde auf Grundlage von Simulationsdaten des Umformprozesses (FE-Prozessanalyse) in Einzelsegmente geteilt und mit entsprechenden Verbindungs- und Fügestellen versehen. Die Einzelteile wurden spanend gefertigt, montiert und zur Überbrückung der Segmentspalte durch ein Laser-Pulver-Auftragsschweißverfahren oberflächlich gefügt. Die Endkontur wurde durch spanende Nachbearbeitung – insbesondere der Nahtstellen – erreicht. Als Abschluss des Proof of Concept wird das gefertigte Werkzeug im nächsten Schritt in einem Tiefziehprozess eingesetzt und mit den Fertigungsergebnissen eines Monoblock-Werkzeugs verglichen. Herausforderungen sind dabei vor allem die Gesamtfestigkeit des Werkzeugs sowie die Härteunterschiede zwischen Grundwerkstoff und Schweißnaht.
Im Anschluss an die Überprüfung des vorgestellten Konzepts ist eine Überführung des Ansatzes in die industrielle Anwendung vorgesehen. Bei Anregungen und Fragen stehen wir daher gerne zur Verfügung! Vor allem hinsichtlich Schaffung von Anknüpfungspunkten an die industriellen Bedarfe – aber auch um die Integration weiterer Anwendungsbereiche in die vorgeschlagene Lösung zu stützen.
Titelbild: © Fraunhofer IWU/ Christian Hermeling
Kommentar hinzufügen