Welche Methoden der VIBN gibt es denn eigentlich?
Durch den Einsatz der Virtuellen Inbetriebnahme wird mit Hilfe von physikalisch basierten digitalen Zwillingen von Maschinen und Anlagen die Entwicklung von Steuerungscode unterstützt und damit die Inbetriebnahme von Produktionsanlagen beschleunigt.
Dabei werden vor allem drei Simulationskonfigurationen eingesetzt: Model-in-the-Loop (MiL), Software-in-the-Loop (SiL) und Hardware-in-the-Loop (HiL). Sie kommen jeweils in unterschiedlichen Phasen während des Entwicklungsprozesses zur Anwendung. Während bei der MiL modellinterne Logiken verwendet werden, um damit die grundsätzliche Funktionsweise der Steuerungslogik zu testen, wird bei SiL und HiL mit der realen Steuerungslogik gearbeitet. Wobei bei SiL Simulationen eine virtuelle Steuerung und bei der HiL Simulation die reale Steuerungshardware zum Einsatz kommt.
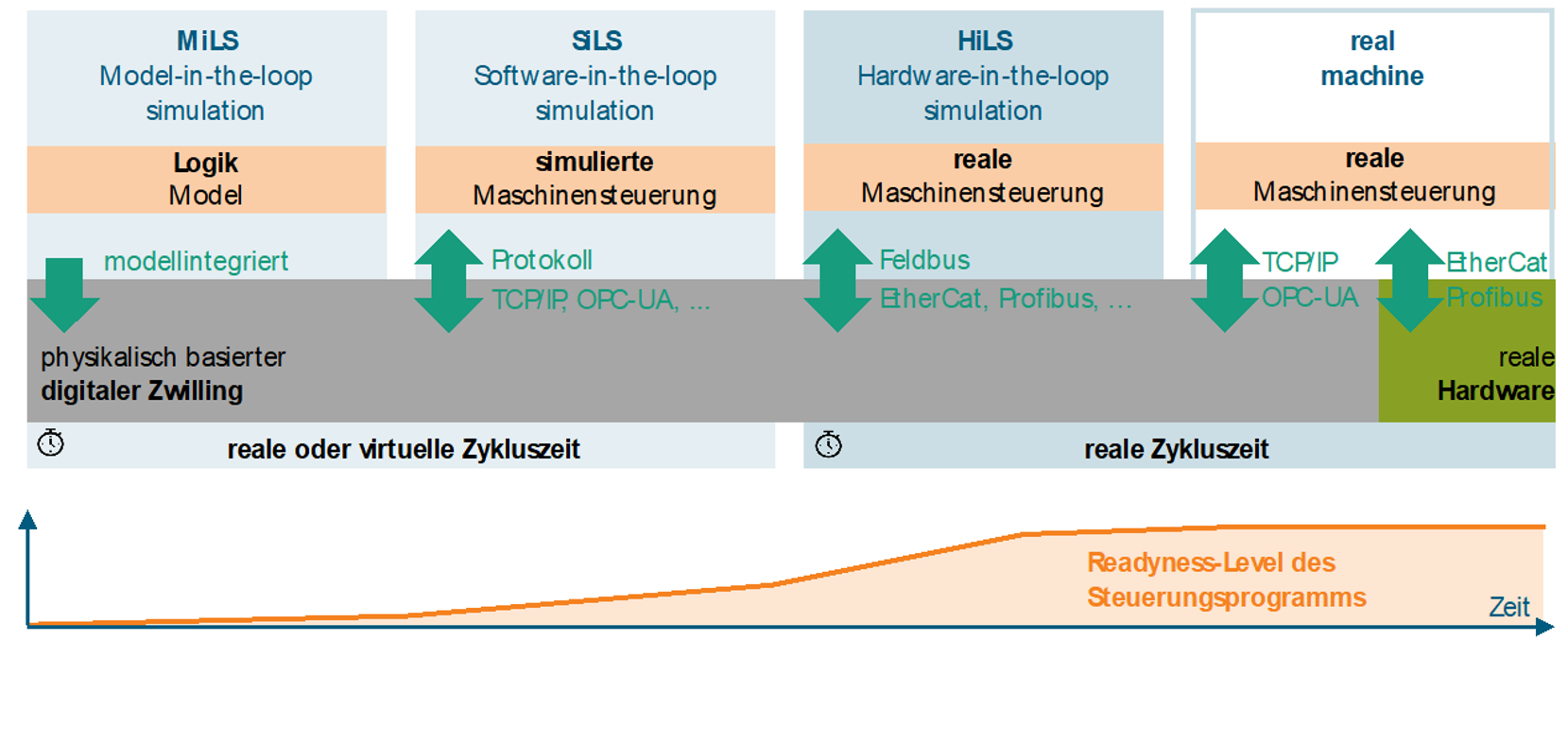
Ein hausgemachtes Anwendungsbeispiel
Doch wie genau läuft das ab? Nun, das lässt sich am besten an einem Beispiel verdeutlichen: Am Fraunhofer IWU wird ein Industrieroboter des Typs Comau NJ-130-2.05 für die Fräsbearbeitung von Bauteilen eingesetzt. Als im vorletzten Jahr das gesamte Versuchsfeld umzog, musste auch der Roboter inklusive Zelle mit. Zu dieser Zeit sollte aber auch ein neuer automatischer Werkzeugwechsler in die Anlage integriert werden, der den automatisierten Wechsel zwischen einem Greifer und einem Fräsers ermöglichen sollte. Doch bis die Hardware einer Roboter-Zelle nach so einem Umzug wieder im Einsatz ist, kann ganz schön viel Zeit vergehen.
Und da kam die virtuelle Inbetriebnahme ins Spiel. Ohne funktionierende Hardware ist die stetige Weiterentwicklung der Software für die Integration neuer Funktionen und die Fehlerbehebung nur eingeschränkt möglich. Durch den Einsatz des digitalen Zwillings und der VIBN, kann der Steuerungs-Code dennoch weiterentwickelt und die Integration neuer Hardware virtuell getestet werden. Selbige Lösungsidee gilt auch, wenn die Hardware aktuell nicht lieferbar ist, wie die Kollegen in diesem Beitrag berichteten.
Ein Modell für jeden Zweck?
Nun stellt sich die Frage, wie diese verschiedenen Simulationskonfigurationen konkret zum Einsatz kommen können. Dazu kommen wir zurück zum Beispiel des automatischen Werkzeugwechslers: Die einfach einzurichtende MiL half in einem frühen Stadium eine gute Position für den Werkzeugbahnhof in der Zelle zu bestimmen. Während mit groben Positionsvorgaben in Control Panels die Erreichbarkeit der abgelegten Werkzeuge durch den Roboter überprüft werden konnte, konnten die Bewegungen zum Aufnehmen und Ablegen der Werkzeuge, durch die Vorgabe von Punktelisten, auf Kollisionen überprüft werden. Danach konnte damit begonnen werden den Werkzeugwechsel in Form von Code in die bereits bestehende Steuerungslogik zu integrieren. Klingt im ersten Moment nicht allzu schwierig, oder?
In der Realität sieht das aber anders aus: Um den Werkzeugwechsel automatisiert ablaufen lassen zu können, muss der Roboter nicht nur in der richtigen Abfolge verschiedene Positionen anfahren, sondern es müssen auch verschiedene pneumatische Ventile angesteuert und Signale von der Sensorik verarbeitet werden. Wenn dann auch noch, wie in unserem Fall, die Hardware fehlt oder noch nicht verwendet werden kann, ist ein Test des eigenen Codes nicht möglich. Dies führt dann dazu, dass die ganzen Fehler bei der eigentlichen Inbetriebnahme gesucht und beseitigt werden müssen, denn aus dem Stehgreif ohne Test einen perfekt funktionierenden Code zu entwickeln, ist schlichtweg sehr unrealistisch.
Um diesem Problem vorzubeugen, wurde der neue Steuerungscode im Rahmen von SiL und HiL zunächst gegen das Modell getestet. Logik-Fehler in Bezug auf die Signalabfrage, Ventilschaltung und Bewegungsabfolge des Roboters konnten so bereits vor der realen Inbetriebnahme erkannt und beseitigt werden. Außerdem kann im Modell per Knopfdruck zwischen den Simulationskonfigurationen gewechselt werden. Dadurch kann es auch für die Integration zukünftiger Anpassungen an der Roboter-Zelle verwendet werden. Die einfache Umschaltung ermöglicht dabei einen flexiblen Einsatz der verschiedenen Konfigurationen im Entwicklungsprozess.
Was hat das ganze mit Ihnen zu tun?
Wir können festhalten: die Anwendung der VIBN in all ihren Spielarten auf die Problemstellung des Werkzeugwechslers hat es uns ermöglicht, eigentlich sequenziell ablaufende Phasen der Inbetriebnahme zu parallelisieren und so viel Zeit zu sparen. Wir konnten zeigen, dass es gelungen ist, ein einziges generisches Modell zu entwickeln, das mithilfe der verschiedenen Simulationsmethoden in der Lage ist unterschiedlichste Problemstellungen zu bedienen, von der Überprüfung der Steuerungslogik über Erreichbarkeitsuntersuchungen samt Kollisionskontrollen bis hin zur Durchführung virtueller Fräsversuche.
Wenn auch Sie in dem beschriebenen Szenario eine vertraute Herausforderung erkennen und diese mit kompetenter Unterstützung in Sachen VIBN angehen wollen, nehmen Sie gern Kontakt mit uns auf. Wir helfen gern! Unser Kollege Herr Christian Gollee steht Ihnen unter folgender Mailadresse gerne für Rückfragen zur Verfügung: christian.gollee@iwu.fraunhofer.de.
Headerbild: © Fraunhofer IWU