Einordnung
Metallbauteile verstecken sich in einer Vielzahl von Produkten des täglichen Gebrauchs, wie z. B. in Automobilen oder Elektrowerkzeugen. In diesen Bereichen, in denen präzise und belastbare Bauteile gefordert sind, ist die spanende Fertigung mit Werkzeugmaschinen meist alternativlos.
Trotz der hohen Widerholgenauigkeiten von Werkzeugmaschinen führen verschiedene Mechanismen zu Abweichungen zwischen dem geplanten und realen Bauteil. Die prominentesten Effekte sind z. B. Werkzeugverschleiß, Rattern oder thermisch bedingte Bearbeitungsfehler.
Wie genau die Fehler entstehen und sich zusammensetzen ist nicht einfach vorherzusagen. Anwender betreiben daher hohe Aufwände beim Einfahren der Prozesse und unterziehen die gefertigten Bauteile einer Qualitätskontrolle. Beides verursacht Mehrkosten, welche nicht zur Wertschöpfung beitragen.
Das Projekt AccuMonit nimmt sich genau dieser Problemstellung an und versucht die Mehraufwände für die Qualitätssicherung zu senken, in dem prozessbegleitend Maschinen- und Sensordaten erfasst werden. Mittels der erfassten Daten wird der Bearbeitungsprozess anschließend „Reverse Engineered“, um potenzielle Bearbeitungsfehler bereits in den Daten erkennen zu können.
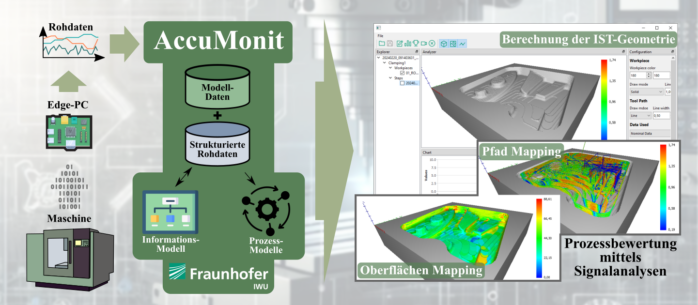
Das Vorgehen
Mittels IoT-Geräten oder EDGE-Devices werden hochfrequente Maschinendaten erfasst und strukturiert abgelegt. Dies erlaubt die automatisierte Anwendung von Prozessmodellen, durch welche die rohen Daten in technologisch relevante Daten überführt werden können. Eines der wichtigsten Modelle ist die Abtragssimulation, welche die Bestimmung der resultierenden Bauteilgeometrie auf Basis der Ist-Positionen erlaubt.
Da die über den Encoder erfassten Positionen i. d. R. nahe am Motor gemessen werden, entspricht der Messwert nicht exakt der Position an der Werkzeugspitze. Um diese Abweichung zu bestimmen, ist daher ein IMU-Sensor an der Hauptspindel installiert, welcher die Beschleunigung und Orientierung in allen drei Raumrichtungen messen kann. Die gemessenen Größen werden auf eine Verlagerung transformiert und auf die gemessenen Encoder-Positionen addiert, wodurch eine präzise Berechnung der resultierenden Bauteilgeometrie möglich wird. Durch einen Vergleich des geplanten Bauteils mit dem simulierten Bauteil kann der ortsaufgelöste Bearbeitungsfehler bestimmt und visualisiert werden. Der Anwender kann damit auf einen Blick erkennen, ob und wo kritische Abweichungen vorhanden sind, und fehlerhafte Bauteile noch vor einer aufwändigen Vermessung aussortieren.
Die Vision
Die vorgestellte Lösung folgt den Ansätzen eines „Digitalen Zwillings“, welcher die Datenerfassung, Standardisierung und Erweiterung durch Prozessmodelle vorsieht. Im vorgestellten Ansatz wird die Prognose der resultierenden Bauteilgeometrie fokussiert, welche nur eine der unzähligen Möglichkeiten für Prozessmodelle repräsentiert. Weitere Modelle, wie z. B. Zerspankraftmodelle, Werkzeugabdrängungsmodelle oder Modelle zur Materialcharakterisierung werden künftig nachgerüstet, um die Prozessauswertung zu erweitern und weitere technologisch relevante Kenngrößen ableiten zu können, welche auch bei der Auslegung neuer Prozesse eingesetzt werden sollen.
DISCLAIMER
Wir hoffen mit diesem Vorgehen einen Beitrag zur Digitalisierung des Maschinenbaus leisten zu können, und der Industrie ein Werkzeug anzubieten, mit dem Prozesse nebenläufig erfasst und gesichert werden können, um eine Grundlage für datengetriebene Prozessoptimierungen zu schaffen und das Know-How in den Unternehmen zu halten.
Finden Sie den Ansatz interessant oder sind vielleicht in einem ähnlichen Feld tätig? Dan melden Sie sich doch bei uns und wir schauen gemeinsam, wie die digitale Fertigung von morgen aussehen könnte!
eric.wenkler@iwu.fraunhofer.de (Softwarearchitektur & Implementierung), albrecht.haenel@iwu.fraunhofer.de (System-Design & Funktionalität)
hendrik.rentzsch@iwu.fraunhofer.de (Abteilung Werkzeugmaschinentechnik)