viProSys: industrienahe Anlage für tiefgezogene Papierbecher
Mit dieser Fragestellung beschäftigt sich das Projekt viProSys als eine Kooperation des Fraunhofer IWU und der TU Dresden. Das Schlüsselkonzept, um den komplexen Tiefziehprozess von Papierbechern wirtschaftlich zu nutzen, ist dabei die „virtuelle Inbetriebnahme intelligenter Produktionssysteme“. Dieses Konzept wird im Rahmen des Projekts viProSys entwickelt und ist perspektivisch auf diverse komplexe Fertigungsprozesse übertragbar. Im Blogbeitrag „Das Projekt viProSys hat die Mission, die Fehlerrate in der Kartonbecherproduktion zu verringern“ finden sie einen Überblick über alle Komponenten und Schritte der virtuellen Inbetriebnahme. In diesem Beitrag hier wird detaillierter auf die Simulation des Tiefziehvorgangs von Papier und das Training eines neuronalen Reglers als konkrete Bestandteile der virtuellen Inbetriebnahme einer Papierbecheranlage eingegangen. Diese industrienahe Anlage soll befähigt werden, prototypische Kleinserien versiegelter tiefgezogener Papierbecher gemäß industriellen Anforderungen herzustellen.
Durch das Tiefziehen von einseitig mit PE beschichtetem Papier können perspektivisch Becher, Schalen und Trays in vielfältigen Geometrien als Verpackung für zahlreiche Lebensmittel gefertigt werden. Dabei sind Trays offene Verpackungsmittel, in dem sich mehrere Einzelverpackungen befinden. Vorbild für den Fertigungsprozess ist das Tiefziehen von Metall. Hierbei handelt es sich um einen gut erforschten und in der Industrie weit verbreiteten Umformprozess. Das Vorgehen lässt sich jedoch nicht unverändert übertragen, denn Papier als faserbasiertes Material besitzt eine deutlich geringer ausgeprägte Fähigkeiten als Metall, sich dauerhaft zu verformen. Daher kann beim Tiefziehen von Papier anders als bei Metall die Faltenbildung nicht vermieden werden, sondern muss gezielt gesteuert und genutzt werden, um die gewünschte Form und Stabilität der Becher zu erreichen.
Um die Umformeigenschaften des Papiers zu verbessern, wird im Projekt viProSys mit gezielter Befeuchtung des Materials und beheizten Werkzeugen gearbeitet. Diese Maßnahmen können eingesetzt werden, um die Becher in einer ausreichenden Qualität herzustellen. Durch die zwei zusätzlichen Einstellmöglichkeiten ergibt sich jedoch auch ein komplexer Prozess mit zahlreichen, voneinander abhängigen Prozessparametern. Diese müssen zudem während der automatisierten Fertigung immer wieder neu eingestellt werden, da Papier stärker in seinen Grundeigenschaften variiert als zum Beispiel Metall und vermehrt auf Umwelteinflüsse reagiert. Die Stabilisierung des Prozesses und die Optimierung der Prozessparameter an der realen Anlage mittels Trial-and-Error sind schwer realisierbar, da selbst bei großem Zeiteinsatz nicht alle Parameterkombinationen getestet werden können.
Intelligente Steuerung als Schlüsselkonzept
Deshalb wird im ersten Schritt eine Finite-Elemente-Simulation (FE-Simulation) erstellt, welche den Umformprozess vollständig abbilden soll. Insbesondere die korrekte Abbildung der Faltenbildung ist dabei herausfordernd und numerisch schwer zu stabilisieren. Die FE-Simulation wird mit experimentellen Daten aus Ersatzversuchen kalibriert, bis sie die Becherqualität und die Grenzen des Prozesses für einen breiten Parameterbereich korrekt abbildet. Diese Berechnungen sind jedoch zeitaufwändig und können bei dem geplanten Prozesstakt von bis zu 60 Hub/ Minute nicht die geforderten Echtzeit-Vorhersagen treffen, um in die Steuerung integriert zu werden.
Daher wird im zweiten Schritt das sogenannte Technologieregelungsmodell (TRM) auf den Simulations- und experimentellen Daten trainiert. Das ist ein Machine-Learning-Modell, welches anhand des aktuellen Zustandes des Papiers und der geplanten Prozessparameter die Anzahl und die Verteilung der Falten voraussagt. Anhand dieser Größen wird die Qualität der Becher bewertet. Im realen Prozess wird die Faltenanzahl automatisiert durch einen Algorithmus bestimmt, welcher Fotos von den Bechern auswertet. Das TRM wird nach dem erfolgreichen Training in den Digitalen Zwilling für die virtuelle Inbetriebnahme und später in die reale Steuerung der Papierbecheranlange eingebunden. Für jeden Hub berechnet es eine Prognose. Liegen Faltenzahl und -verteilung innerhalb vorgegebener Bereiche, bleiben die Prozessparameter an der Anlage konstant. Prognostiziert das TRM jedoch eine schlechte Qualität – weil durch eine Änderung des Ausgangszustandes des Papieres die aktuellen Prozessparametern nicht mehr angemessen sind – werden die Prozessparameter im nächsten Hub neu eingestellt. Hierfür läuft eine Optimierung über das Prozessmodell, welche für die aktuelle Papierbeschaffenheit die optimalen Einstellungen findet. Die Papierbecheranlage ist dabei mit zahlreichen Sensoren ausgestattet, um zum einen die aktuellen Feuchtigkeits- und Temperaturwerte in die Bestimmung der Prozessparameter einfließen zu lassen und zum anderen die während der Umformung auftretenden Kräfte und die resultierende Becherqualität zu speichern. Diese Datenpunkte werden in die Steuerung aufgenommen und bei nachfolgenden Einstellungen der Prozessparameter berücksichtigt, wodurch eine intelligente Steuerung entsteht.
Aktueller Stand und zukünftige Schritte
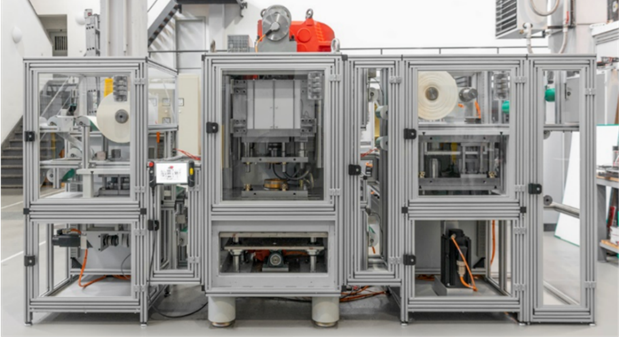
Die industrienahe Fertigung der Papierbecher wird auf einer Papierbecheranlage am Fraunhofer IWU erprobt. Ausführliche Informationen zu dieser Anlage finden Sie ebenfalls im Beitrag „Das Projekt viProSys hat die Mission, die Fehlerrate in der Kartonbecherproduktion zu verringern“.
Im Rahmen des Projekts viProSys wurde bereits eine FE-Simulation des Tiefziehvorgangs aufgesetzt, welche in ihrem Aufbau an FE-Simulationen für das Tiefziehen von Metall angelehnt ist. Insbesondere wird als erster Ansatz ein für Metall konzipiertes Materialmodell verwendet, das mit Ersatzversuchen (vorwiegend Zugversuche und Streifenzugversuche) für das spezifische Papier aus dem Projekt viProSys kalibriert wurde. Der große Vorteil in der Verwendung dieses Materialmodells ist, dass im Vergleich zu papierspezifischen Materialmodellen deutlich weniger Parameter durch Ersatzversuche bestimmt werden müssen. Trotz der getroffenen Vereinfachungen zeigt die FE-Simulation im Abgleich mit manuell tiefgezogenen Papierbechern vielversprechende Ergebnisse. Die Abhängigkeit der Materialkennwerte (Reibkoeffizienten, Fliesskurven, E-Modul etc.) von den Prozessparametern Temperatur und Befeuchtungsmenge wurde in die FE-Simulation integriert. Die resultierenden qualitativen Unterschiede in Faltenzahl und -verteilung in der Simulation entsprechen für die bisher zur Verfügung stehenden Punkte im Parameterraum den manuell tiefgezogenen Papierbechern.
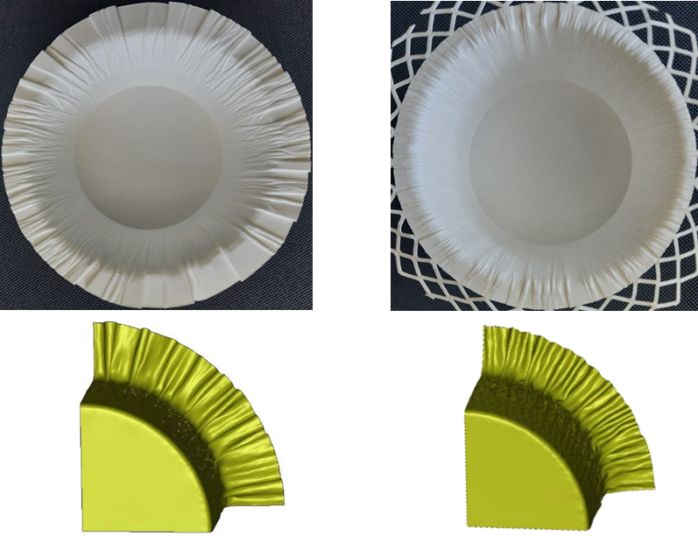
Nach erfolgreicher Kalibrierung für eine breiten Versuchsplan mit Variation von Werkzeugtemperatur, Befeuchtungsmenge und Niederhalterkraft kann ein TRM auf den Simulationsdaten trainiert werden. Für die Qualität der Prognosen dieses TRM hat auch die Datenvorverarbeitung eine große Bedeutung. Das TRM soll Faltenzahl- und Verteilung ausgedrückt in zwei bis drei Zahlen prognostizieren. Das bedeutet, es braucht für das Training genau diese Informationen für jeden Datensatz. Die Ergebnisse der FE-Simulation beinhalten diese Informationen jedoch nur indirekt. Direkt enthalten ist die Bauteilgeometrie des Bechers inklusive der Position und der Form der Falten. Mit Hilfe dieser Werte wird eine Draufsicht des Bechers erstellt. Diese wird von demselben Faltenzähl-Algorithmus ausgewertet, der auch in der realen Anlage eingesetzt wird. Die Ergebnisse des Faltenzähl-Algorithmus werden anschließend dem TRM zusammen mit den zu Grunde liegenden Prozessparametern zur Verfügung gestellt. Die Algorithmen zur Datenvorverarbeitung sind bereits vollständig implementiert.
Fazit
Im industriellen Maßstab durch Tiefziehen hergestellte Papierbecher haben das Potential, zahlreiche Kunststoffverpackungen wirtschaftlich zu ersetzen. Die Papierbecheranlage aus dem Projekt viProSys wird die Möglichkeit bieten, für beispielhafte Geometrien einen stabilen Prozess einzustellen und Kleinserien testweise herzustellen. Das TRM und die darüber laufende Optimierung sind hierbei die entscheidenden Maßnahmen, um die Prozessparameter zu identifizieren, mit denen stabile, dichte Becher hergestellt werden können. Weiterhin sorgen das TRM und die Optimierung, welche zusammen in einer intelligenten Steuerung münden, dafür, dass die Becherqualität auch bei einem Prozesstakt von bis zu 60 Hub/ Minute kontinuierlich sichergestellt wird. So entsteht ein hochproduktiver Prozess, der für geringe Produktionskosten und -zeit sorgt, wodurch viProSys einen Beitrag zur Erreichung der Marktreife von nachhaltigeren Verpackungslösungen leisten kann.
Sie haben Fragen oder Anmerkungen? Unsere Kollegin Frau Klara Liesegang steht Ihnen gerne unter folgender Mailadresse zur Verfügung: klara.liesegang@iwu.fraunhofer.de.
Headerbild: © Fraunhofer IWU