In der Regel werden die Wartungsintervalle und Lebensdauer kritischer Komponenten von CNC-Maschinen bereits vor der eigentlichen Nutzungsphase der Maschine festgelegt. Während der Konstruktion werden diese Größen auf Basis einer Abschätzung der zukünftigen Betriebszustände wie mittlere Drehzahl, durchschnittliche Belastungen und Umgebungsbedingungen berechnet (siehe z.B. DIN ISO 281).
Die realen Betriebszustände können von den in der Maschinenauslegung angenommenen Werten für mittlere Drehzahlen und Belastungen jedoch stark abweichen. Dies kann dazu führen, dass der Verschleiß einiger Komponenten wesentlich geringer ist als gedacht und vorher festgelegte Wartungsintervalle oder Intervalle für Komponententausch unnötig sind. Umgekehrt ist es möglich, dass der Verschleiß einiger kritischer Führungen und Lager zum Teil deutlich erhöht und die Lebensdauer entsprechend gering ist. In diesem Fall steigen die Instandhaltungskosten stark an.
Digitaler Zwilling ermittelt die Restlebensdauer auf Basis realer Betriebszustände
Im digitalen Zwilling zur Bestimmung der Restlebensdauer von CNC-Maschinen werden zu jedem Zeitpunkt die realen Betriebszustände der Maschine erfasst (vgl. Abbildung 1). Mit Hilfe der Achsmesssysteme werden die realen Verfahrwege der Führungen und Lager bestimmt. Parallel dazu werden über ein Metamodell nach dem Prinzip eines virtuellen Sensors die jeweils momentanen Belastungen der kritischen Komponenten berechnet. Diese beiden Größen werden zusammen mit weiteren Parametern genutzt, um die Restlebensdauer der kritischen Komponenten auf Basis der realen Betriebszustände mit den bekannten empirisch erprobten Zusammenhängen zu ermitteln.
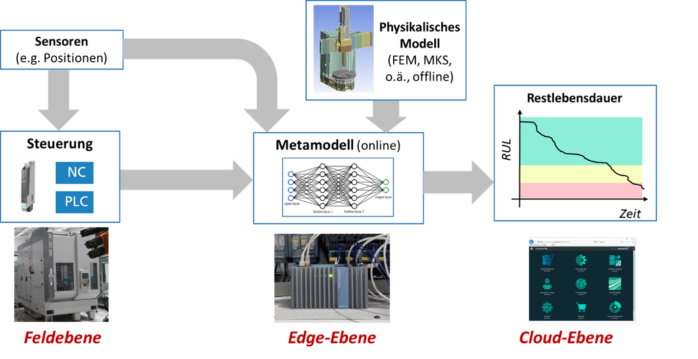
Der digitale Zwilling ermöglicht die vorrausschauende Planung von Instandhaltungsmaßnahmen und dadurch eine Reduktion von Maschinenstillstandzeiten. Andererseits sind auf Basis des digitalen Zwillings bei Bedarf auch Anpassungen der Bearbeitungszyklen möglich, um die Belastungen auf kritische Komponenten zu verringern und deren Lebensdauer zu erhöhen.
Virtuelle Sensoren als Enabler des digitalen Zwillings
Kernkomponente der vorgestellten Lösung ist die Bestimmung der momentanen Belastungen auf kritische Komponenten der CNC-Maschinen. Diese Belastung wird mit virtuellen Sensoren ermittelt. Im virtuellen Sensor werden reale Sensordaten der Maschine als Eingangsdaten genutzt und die Ausgangsgrößen über ein Modell live berechnet. Um diese vergleichsweise komplexe Berechnung online während des Betriebs der Maschine durchzuführen, wird ein Metamodell aus dem Bereich maschineller Lernverfahren benutzt. Das wesentlich effizientere datenbasierte Metamodell wird im Vorfeld auf Basis von Simulationsdaten eines physikalischen Maschinenmodells (FEM- oder Mehrkörpersimulation) aufgebaut und angelernt (vgl. Abb.2). Das physikalische Maschinenmodell ist nicht onlinefähig. Allerdings ermöglicht das reduzierte Metamodell die Berechnung der momentanen Belastungen und die Bestimmung der Restlebensdauer kritischer Komponenten. Das geschieht über das Konzept des virtuellen Sensors.
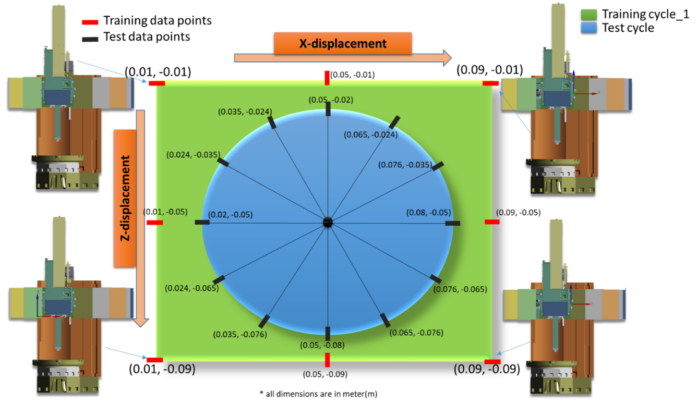
Der Digitale Zwilling ermöglicht dem Anwender Toshulin eine zielgerichtete Wartung seiner Maschinen und Anlagen. Alles was man dafür benötigt ist ein Gateway zur Erfassung der aktuellen Maschinendaten und für die Implementierung des Metamodells. Die Informationen zur Restlebensdauer aus dem Digitalen Zwilling kann über das Gateway an einen Server im Unternehmen oder eine Cloud-Lösung weitergeleitet werden.
Entwicklung im Rahmen des Level-UP Projektes
Die vorgestellte Lösung wurde im Rahmen des Level-UP Projektes entwickelt und an einer Vertikaldrehmaschine des Projektpartners Toshulin demonstriert.
Level-UP ist ein Forschungsprojekt, welches von der EU im Rahmen des ‚Horizon 2020 research and innovation programme‘ gefördert wird (Grant Agreement Number 869991). Ziel des Projektes ist die Erhöhung der Restlebensdauer großer und kapitalintensiver Produktionsanlagen. Das geschieht über die Entwicklung innovativer Lösungen im Bereich der Diagnose, Vorhersage, Modernisierung, Reparatur Wiederaufarbeitung und Digitalisierung. Weitere Infos zum Level-UP Projekt finden Sie hier:
http://www.levelup-project.eu/
https://www.linkedin.com/in/level-up-eu-project-270543196/
https://www.youtube.com/channel/UC55PzRO38XdDWvBOtuPiHjQ
https://twitter.com/levelup_eu
Smart Maintenance Community
Dieser Beitrag stellt eine Möglichkeit der prädiktiven Instandhaltung vor. Weitere Ansätze und Lösungen mit ähnlichen Zielstellungen werden in der Smart Maintenance Community umgesetzt. Die wichtigsten Eckdaten dieses Zusammenschlusses von derzeit 12 Fraunhofer-Instituten und eine Vorstellung der verschiedenen Level von Instandhaltungsstrategien lesen Sie in unserem Auftaktbeitrag zum Thema der Smart Maintenance Community hier.
Für Rückfragen und Anmerkungen steht Ihnen Herr Dr. Andreas Otto als Gruppenleiter “Virtuelle Sensorik und Maschine-Prozess-Interaktion” gerne unter folgender Mailadresse zur Verfügung: andreas.otto@iwu.fraunhofer.de.
Headerbild: © Fraunhofer IWU